Opening an Industrial Facility? Here Are the Key Factors to Consider
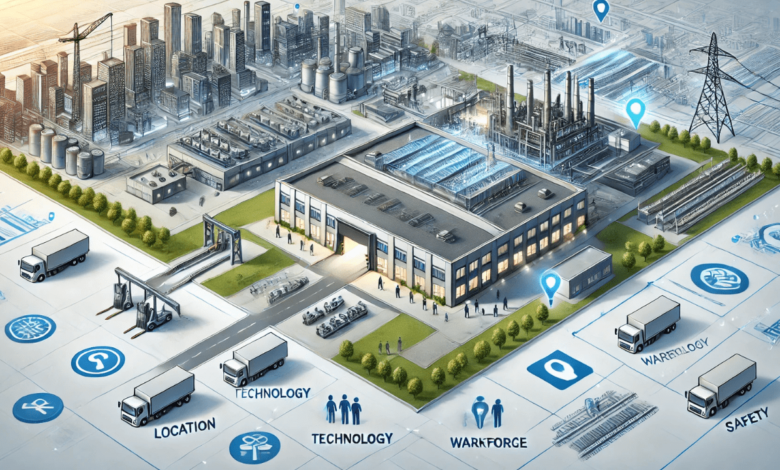
Opening an industrial facility is an exciting and ambitious venture. Whether you’re starting a manufacturing plant, warehouse, or distribution center, the success of your facility hinges on a combination of careful planning, strategic decision-making, and risk management. Before diving into the project, it’s essential to understand the various factors that can significantly impact the long-term success of your industrial operation. Here are the key factors you must consider before opening your industrial facility.
1. Location, Location, Location
The location of your industrial facility plays a crucial role in its efficiency and overall success. When choosing the site, you need to consider a variety of factors, such as proximity to suppliers, access to transportation networks, labor availability, and local zoning regulations.
- Proximity to Suppliers and Clients: Being close to your suppliers can reduce transportation costs and ensure timely deliveries of raw materials. Additionally, proximity to clients can enhance your ability to serve them efficiently, reducing shipping time and costs.
- Transportation Accessibility: A well-connected location is essential for smooth operations. Look for an area with easy access to highways, railroads, or ports, depending on your mode of transportation. If your facility relies on international shipping, being close to a port or airport is an added advantage.
- Labor Availability: Ensure the area has a skilled workforce to meet your operational needs. If the location is in a rural area, you might need to consider offering competitive wages or relocation packages to attract qualified employees.
- Zoning and Regulations: Before finalizing the location, check the local zoning laws to ensure the area is approved for industrial use. You’ll also want to investigate any environmental regulations or restrictions that might impact your facility’s operations.
2. Building Design and Layout
The design and layout of your industrial facility are pivotal in ensuring smooth and efficient operations. A well-organized space will maximize productivity, minimize waste, and enhance employee safety.
- Flow of Materials: When designing your facility, plan for the optimal flow of materials from the moment they enter the facility to the final product or shipment. Minimize unnecessary movement and ensure materials pass through a logical progression to reduce inefficiencies.
- Storage and Space Planning: Consider the amount of space required for storing raw materials, finished products, and equipment. If your operations involve heavy machinery, ensure the building can accommodate large equipment and that it’s easily accessible.
- Future Expansion: While you may have a clear idea of your current space needs, it’s essential to plan for future growth. Design your facility with the flexibility to expand as your business evolves, whether by adding more production lines, increasing storage space, or expanding office areas.
3. Permits and Licensing
Operating an industrial facility requires compliance with various local, state, and federal regulations. Ensure you have all necessary permits and licenses in place before you begin operations. These may include environmental permits, building permits, health and safety certifications, and business licenses.
- Environmental Compliance: Many industrial facilities must comply with environmental regulations, including waste disposal, air quality control, and water usage. In Idaho, it’s crucial to familiarize yourself with the state’s specific requirements, such as the Stormwater Pollution Prevention Plan (SWPPP), alongside federal regulations like those from the Environmental Protection Agency (EPA), to ensure your facility meets all legal standards governing industrial activities.
- Safety Regulations: The Occupational Safety and Health Administration (OSHA) sets stringent guidelines for workplace safety. Your facility must meet OSHA standards to ensure employee safety, prevent accidents, and avoid costly fines.
4. Technology and Automation
In today’s competitive industrial landscape, adopting the latest technology and automation tools can significantly boost your efficiency and profitability.
- Automation: Depending on your industry, automation can streamline operations, reduce labor costs, and increase output. Whether it’s automated production lines or inventory management systems, investing in automation technology can lead to long-term savings.
- Technology Integration: Ensure your facility is equipped with the necessary technology to monitor production, track inventory, and analyze operational data. Integrating software systems such as Enterprise Resource Planning (ERP) and Manufacturing Execution Systems (MES) can optimize your facility’s operations and improve decision-making.
5. Workforce and Training
A skilled and well-trained workforce is critical to the success of your industrial facility. When opening a new facility, it’s essential to attract qualified workers, provide comprehensive training, and foster a positive work environment.
- Hiring and Retention: Attracting the right talent starts with offering competitive wages, benefits, and job security. Once you have your employees, focus on retaining them by fostering a culture of respect, teamwork, and growth opportunities.
- Training Programs: Continuous training programs are necessary to keep your workforce up-to-date on new technologies, safety protocols, and industry standards. Implementing regular training sessions ensures that your employees are well-equipped to meet operational demands and can perform their roles safely.
6. Financial Planning and Budgeting
Opening an industrial facility requires a significant financial investment, and proper budgeting is essential to keep costs in check and ensure long-term profitability. Consider the following:
- Initial Capital Investment: The cost of land, building construction, machinery, and equipment can be substantial. Be sure to account for all costs in your financial plan, including unexpected expenses such as delays or price fluctuations.
- Operational Expenses: Ongoing costs, such as utilities, maintenance, and wages, should be factored into your budget. Monitor these costs closely to ensure you stay within budget and can maximize profitability.
- Return on Investment (ROI): Conduct a thorough financial analysis to estimate your facility’s potential return on investment. Understanding your ROI will help you make informed decisions about funding, expansion, and cost-saving measures.
7. Safety and Security
Safety and security are paramount in any industrial facility. Not only do you need to protect your employees, but you also have to safeguard your assets, equipment, and inventory.
- Workplace Safety: Develop and implement robust safety protocols to protect your employees from workplace accidents. Regular safety audits and drills will ensure your workforce is prepared for emergencies.
- Security Systems: Protect your facility from theft, vandalism, and unauthorized access by installing security systems such as surveillance cameras, alarms, and access control systems.
In Conclusion
Opening an industrial facility is a complex process that requires thorough planning, resource allocation, and risk management. By carefully considering factors such as location, design, permits, technology, workforce, and finances, you’ll set your facility up for success and ensure it operates efficiently for years to come.